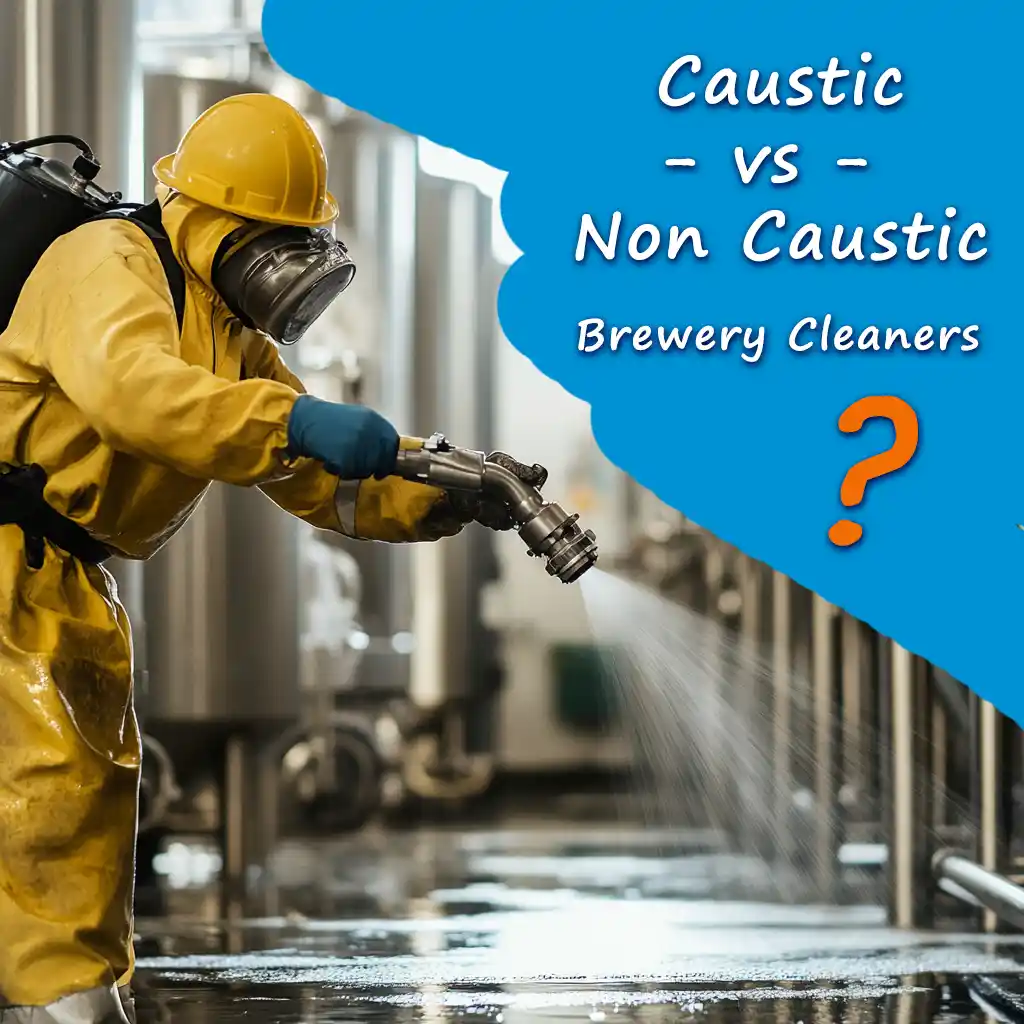
In the brewing industry, cleanliness isn’t just a routine task—it’s the cornerstone of producing high-quality beer. From small-scale homebrewers to large commercial breweries, maintaining impeccable hygiene standards is essential to prevent contamination, preserve flavor integrity, and ensure consumer safety. The array of cleaning solutions available—ranging from caustic and non-caustic alkaline brewery wash, to oxidizing agents—can be overwhelming, each presenting unique benefits and challenges. Understanding these differences is crucial for brewers aiming to optimize their cleaning processes and uphold the highest standards of their craft.
This comprehensive guide delves deeply into the realm of brewery and equipment cleaning, seamlessly blending detailed insights with practical advice. By examining the chemical nuances, environmental impacts, and practical applications of various cleaning agents, brewers are equipped to make informed choices that protect their equipment, ensure safety, and produce superior beer. Whether you’re a homebrewer seeking effective cleaning methods or a professional brewer looking to enhance operational efficiency, this guide provides the knowledge you need to navigate the complexities of brewery hygiene.
Understanding Alkaline Cleaners: The Common Denominator in Brewery Cleaning
Most brewery cleaners are alkaline, meaning they have a pH greater than 7. Alkaline cleaners are essential in brewery hygiene because they effectively break down organic materials like fats, oils, proteins, and carbohydrates—common residues in brewing equipment. This alkalinity makes them a cornerstone in cleaning processes across breweries of all sizes.
By recognizing that alkalinity is a common factor among brewery cleaners, you’ll better understand how each type—caustic, non-caustic, and oxidizing—leverages this property differently to achieve effective cleaning results.
What Does “Alkaline” Mean?
- Substances with a pH above 7.
- Effective at saponifying fats and denaturing proteins.
Why Are Alkaline Cleaners Used in Breweries?
- Excellent at removing organic soils typical in brewing.
- Enhance the action of surfactants and other cleaning agents.
Common Misconceptions Of Caustic vs Non Caustic
Non-caustic cleaners are less effective than caustic cleaners.
Reality: Modern non-caustic cleaners match or exceed the efficacy of caustic cleaners, especially in removing organic residues, biofilms, and even inorganic deposits like beer stone.
Caustic cleaners are always more cost-effective.
Reality: Additional expenses like heating, safety measures, equipment wear, and disposal can make caustic cleaners more costly in the long run.
Only acidic cleaners can remove beer stone.
Reality: Advanced non-caustic cleaners with chelating agents effectively remove beer stone by dissolving calcium deposits without harsh acids.
FAQ – Caustic & Non Caustic Brewery Cleaners
Often, yes. Evaluate your specific needs, as non-caustic cleaners handle most tasks traditionally performed by caustic cleaners, including the removal of organic residues and beer stone.
Through visual inspections, regular microbiological testing, and consistent beer quality without off-flavors.
Review manufacturer guidelines, adjust concentrations as recommended, and ensure staff training on new procedures.
Generally, yes. They are designed to be compatible with various materials but always verify with equipment specifications.
They often require less intensive rinsing, reducing water usage and saving time.
Understanding What Caustic, Non-Caustic, and Oxidizing Brewery Cleaners Are:
Now that we know most cleaners fall under the “Alkaline” umbrella, it’s important to understand their terminology so you can be informed when making decisions that affect your beer’s quality, operational safety, and equipment longevity. Terms like caustic, non-caustic, alkaline, and oxidizing cleaners are often used interchangeably, but they have distinct meanings that significantly impact their application in brewery hygiene.
Using a caustic cleaner on equipment not designed for its corrosive nature can cause costly damage or safety hazards. Conversely, choosing a milder cleaner that’s ineffective against certain residues might result in inadequate sanitation, risking contamination and off-flavors.
By clarifying these terms and understanding each cleaner’s specific roles and characteristics, you can select the most appropriate solutions for your brewery’s needs.
Caustic Cleaners
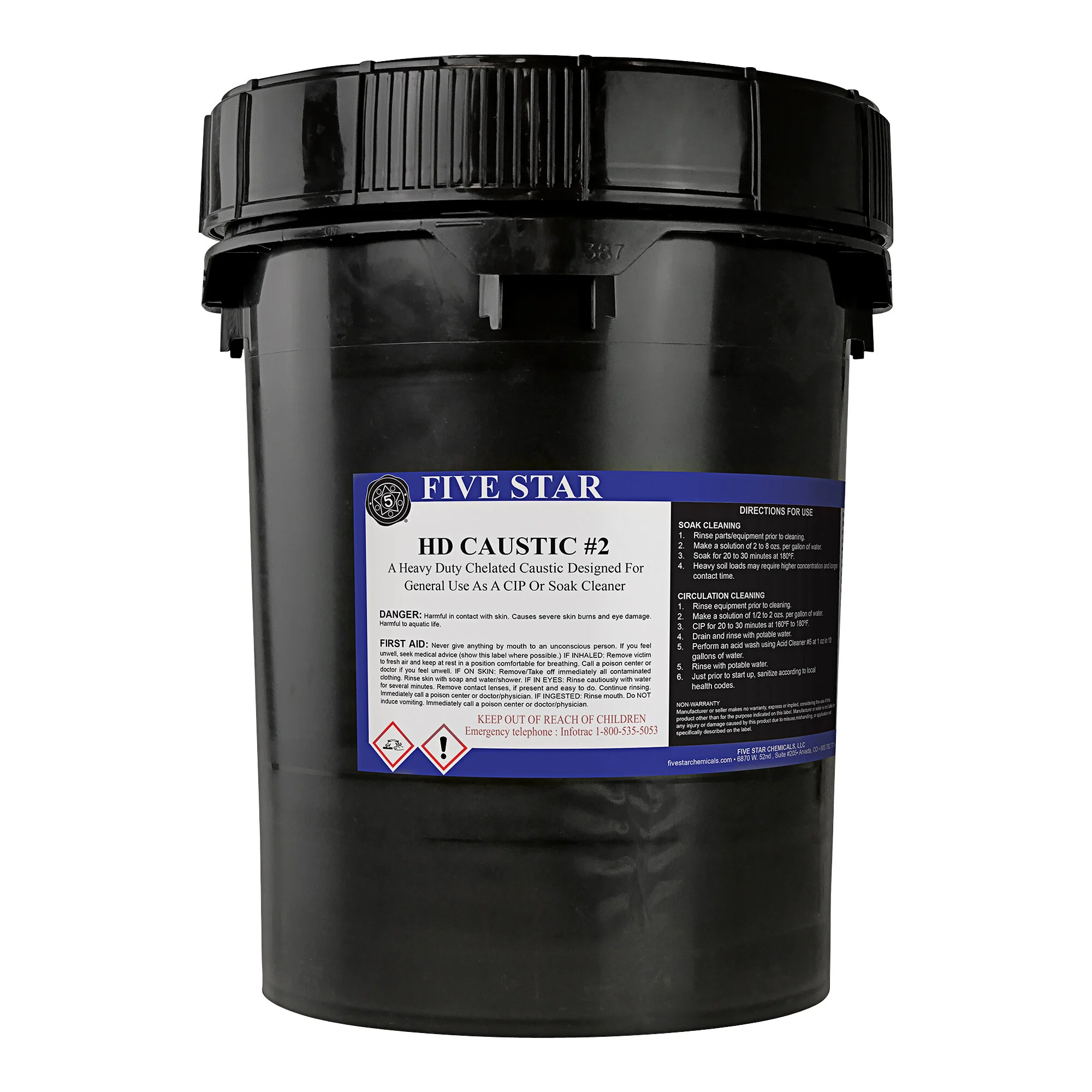
In the brewing industry, “caustic cleaners” specifically refer to strong alkaline cleaners containing caustic agents like sodium hydroxide or potassium hydroxide. These substances are while very effective, are also highly corrosive and can cause chemical burns upon contact with skin or eyes.
Properties:
- High pH Levels: Extremely alkaline, typically with a pH of 13 or higher.
- Reactivity: Highly effective at breaking down organic materials through saponification and protein denaturation.
Usage:
- Heavy-Duty Cleaning: Used for tasks requiring strong chemical action to remove stubborn organic residues.
- Boil Kettles and Heat Exchangers: Historically used for heavy-duty cleaning tasks but may not be ideal due to the drawbacks mentioned.
Pros:
- Powerful Cleaning: Effective at breaking down tough organic materials through saponification.
- Lower Upfront Cost: Generally less expensive per unit compared to formulated non-caustic cleaners.
Cons:
- Requires Heating: Effective cleaning typically requires heating the solution to high temperatures, increasing energy usage.
- Corrosiveness: Can damage the passive layer of stainless steel due to chloride ion impurities, leading to equipment corrosion and stress corrosion cracking.
- Safety Risks: High potential for chemical burns and inhalation hazards; strict safety protocols and protective equipment are essential.
- Ineffective on Beer Stone: Does not remove inorganic deposits like beer stone (calcium oxalate); acidic cleaners are necessary for this task.
- Labor Intensive: May require significant mechanical action (scrubbing) to achieve desired cleanliness levels.
- Environmental Concerns: Disposal requires careful consideration to minimize environmental impact due to high alkalinity and potential toxicity.
Costs and Safety:
Although caustic cleaners are cheaper upfront, the additional costs of energy for heating, potential equipment damage, safety equipment, and labor can offset initial savings. Proper training and safety protocols are essential to mitigate risks.
Non-Caustic Cleaners
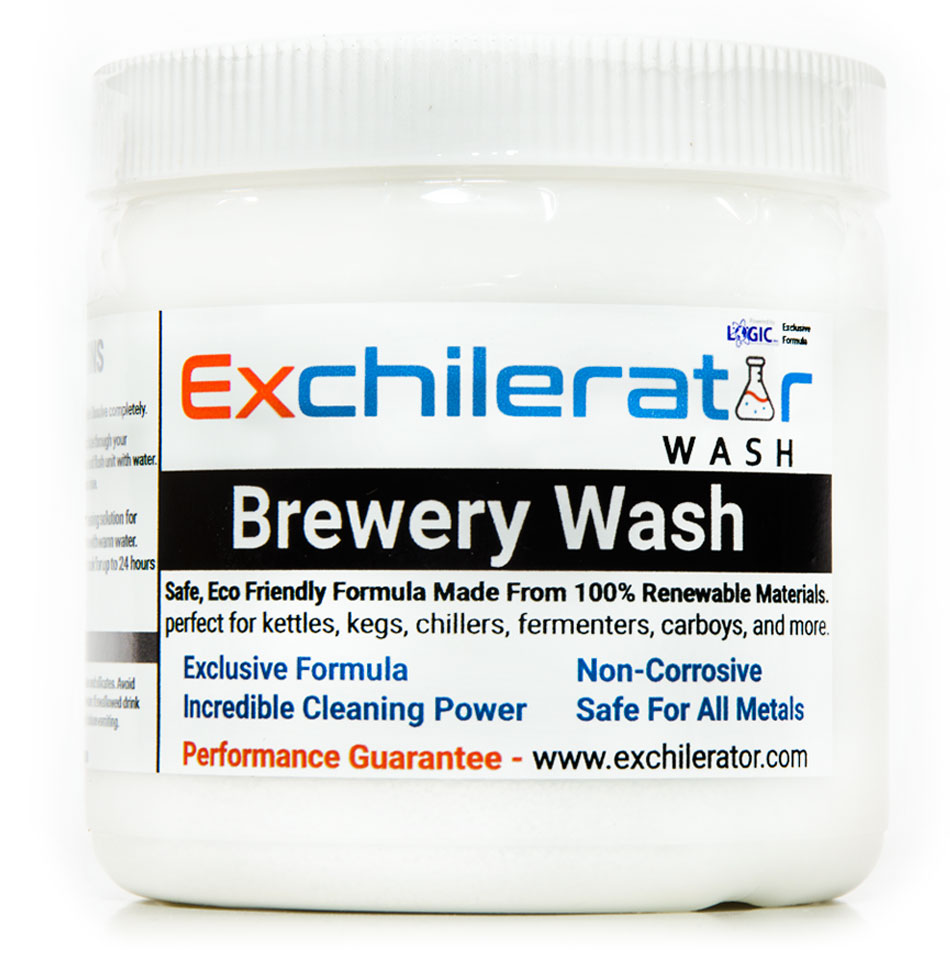
Non-caustic cleaners do not contain strong caustic agents but are still effective through milder alkaline substances and additional components. They offer cleaning power without the extreme corrosiveness of caustic cleaners.
Components and Functions:
- Milder Alkaline Agents: Such as sodium carbonate or sodium metasilicate, providing alkalinity without extreme corrosiveness.
- Sodium Percarbonate: Releases hydrogen peroxide (an oxidizer) and sodium carbonate when dissolved in water.
- Surfactants: Reduce surface tension, allowing the cleaner to penetrate soils and residues more effectively.
- Chelating Agents: Bind to metal ions like calcium and magnesium, helping to dissolve mineral deposits and prevent scale formation.
- Oxidizers: Break down organic compounds through oxidation, enhancing cleaning effectiveness.
- Metal Protectants and Inhibitors: Protect equipment surfaces from corrosion during cleaning.
- Protein Denaturants: Alter protein structures, making them easier to remove.
Properties:
- Moderate to High pH Levels: Alkaline but less extreme than caustic cleaners, usually with a pH between 9 and 12.
- Safer Handling: Less corrosive and pose fewer safety risks compared to caustic cleaners, though proper handling is still necessary.
Usage:
- General Brewery Surfaces: Effective for overall cleanliness, reducing contamination risks.
- Stainless Steel Tanks and Equipment: Cleans without damaging the passive layer, extending equipment life.
- Soft Metals, Plastics, and Rubber Components: Safe for use on hoses, gaskets, seals, and other sensitive materials.
- Beer Stone Removal: Advanced non-caustic cleaners with chelating agents can effectively remove beer stone (calcium oxalate), traditionally removed with acidic cleaners.
Pros:
- Versatility: Effective against a wide range of organic residues.
- Material Compatibility: Safe for use on soft metals, plastics, glass, and gentle on stainless steel’s passive layer.
- Energy Efficiency: Works effectively at lower temperatures (room temperature to ~140°F), reducing energy consumption.
- Deep Penetration: Capable of reaching into small cracks, nooks, and crannies for thorough cleaning.
- Environmental Impact: Formulated with biodegradable components, making it eco-friendly.
- Efficiency: Advanced non-caustic cleaners are potent and often require up to 30% less product per gallon compared to traditional cleaners, reducing costs and environmental footprint.
- Beer Stone Removal: Effective against inorganic deposits like beer stone due to chelating agents that bind to calcium ions.
Cons:
- Higher Concentration May Be Required: Optimal results might necessitate using the cleaner at higher concentrations for certain stubborn soils.
- Cost: Generally more expensive per unit due to the use of high-quality raw materials and advanced formulation.
Costs and Safety:
While non-caustic cleaners may have a higher upfront cost, they can offer long-term savings by reducing energy consumption (no need for heating), lowering labor costs (less scrubbing required), and minimizing equipment wear. Their safer handling properties reduce the need for extensive safety equipment.
Oxidizing Cleaners
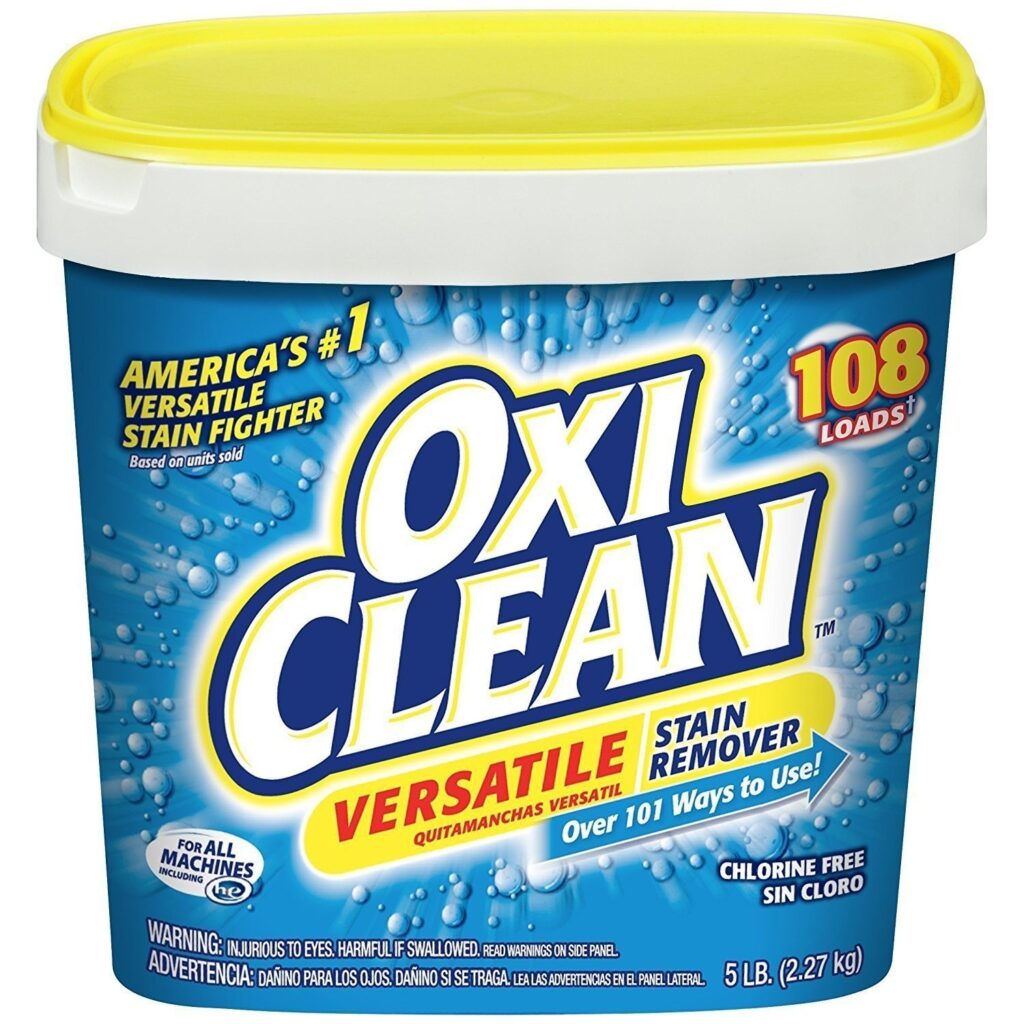
Oxidizing cleaners utilize oxidizing agents, such as hydrogen peroxide, to break down organic compounds through oxidation. They are a subtype of non-caustic cleaners, combining oxidizing action with alkaline properties.
Components and Functions:
- Sodium Percarbonate: Releases hydrogen peroxide and sodium carbonate when dissolved in water.
- Oxidizers: Break down organic residues, stains, and biofilms.
- Milder Alkalinity: Provide effective cleaning without extreme pH levels.
Properties:
- Effective Against Organic Soils: Excellent for removing organic matter and sanitizing surfaces.
- Environmentally Friendly: Break down into water and oxygen, minimizing environmental impact.
- Safety: Less corrosive than caustic cleaners but still require proper handling.
Usage in Breweries:
- General Cleaning: Suitable for cleaning fermenters, hoses, and other equipment where organic buildup occurs.
- Limitations: May not remove inorganic deposits like beer stone without additional agents.
Comparison Table: Caustic vs. Non-Caustic Cleaners
Factor | Caustic Cleaners | Non-Caustic Cleaners |
---|---|---|
Effectiveness | High on organic soils at high temperatures | High on organic soils, biofilms, and beer stone |
Required Temperature | High (often boiling) | Low to moderate (room temp to ~140°F) |
Safety Risks | High (corrosive, burns) | Lower (safer handling) |
Equipment Compatibility | May corrode metals, damage plastics/rubber | Gentle on metals, plastics, and rubber |
Environmental Impact | Potentially harmful, disposal concerns | Biodegradable components, eco-friendly |
Cost | Lower upfront, higher long-term costs | Higher upfront, potential long-term savings |
Impact of Caustic and Non-Caustic Cleaners on Brewing Equipment
Maintaining the integrity of brewing equipment is essential for consistently producing high-quality beer. The choice between caustic and non-caustic cleaners affects not only the effectiveness of your cleaning process but also the longevity and safety of your equipment. Understanding these impacts helps brewers make informed decisions that balance cleanliness with equipment preservation.
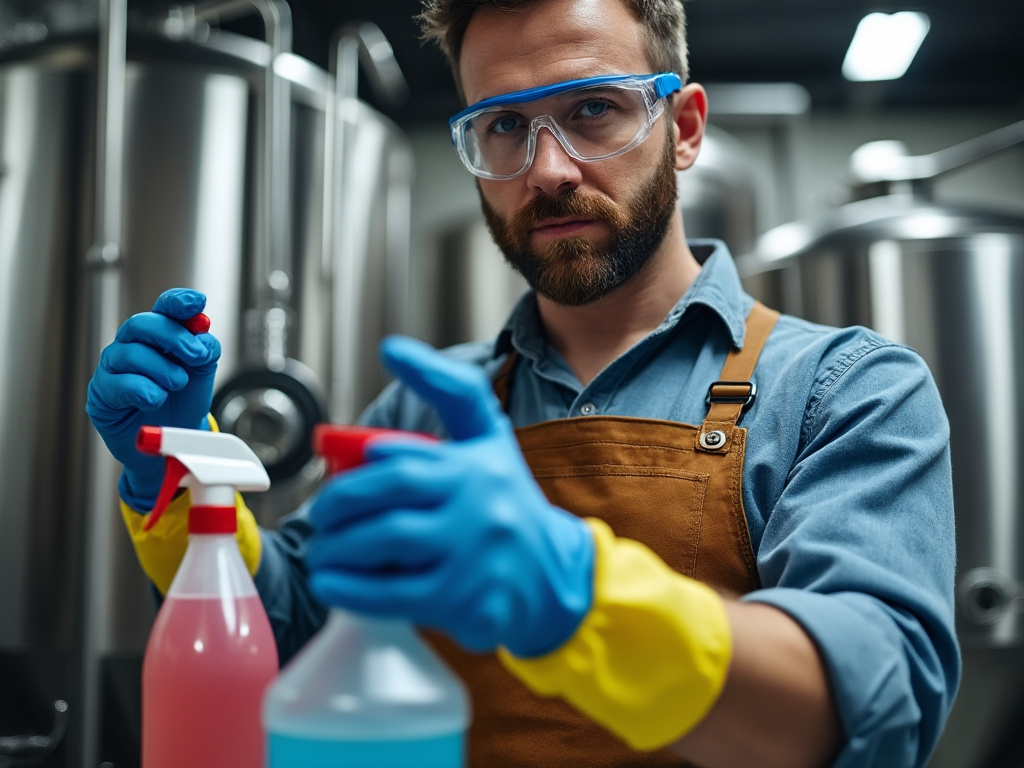
Non-Caustic Cleaners vs. Biofilms
Biofilms are resilient layers of bacteria and other microorganisms that adhere to surfaces within brewing equipment, often resisting standard cleaning methods. Non-caustic cleaners, formulated with surfactants and oxidizers, are particularly effective against these stubborn formations. Surfactants reduce surface tension, allowing the cleaner to penetrate deep into biofilms, while oxidizing agents like hydrogen peroxide break down the organic matrix, effectively dismantling them. This thorough approach ensures a hygienic environment, crucial for consistent beer quality and preventing contamination.
Caustic Cleaners and Biofilms
While caustic cleaners can help remove biofilms by breaking down organic components, they may not be as effective as non-caustic cleaners specifically formulated with surfactants and oxidizers. Non-caustic cleaners are designed to penetrate and dismantle biofilms more thoroughly, making them a preferred choice when biofilm removal is a primary concern.
Caustic Cleaners: Powerful Tools Requiring Careful Handling
Caustic cleaners are widely used in commercial breweries due to their exceptional ability to remove tough organic residues. They are not inherently problematic but require careful handling and adherence to proper usage guidelines.
- Industry Standard: Most commercial breweries routinely use caustic cleaners due to their cost-effectiveness and ability to remove heavy organic soils efficiently. However, they also have established strict protocols and utilize equipment designed for safe caustic use.
- Effectiveness: When used correctly—following manufacturer guidelines for concentration, temperature, and contact time—caustic cleaners are highly effective and safe for equipment designed to withstand them.
However, improper use can pose significant risks:
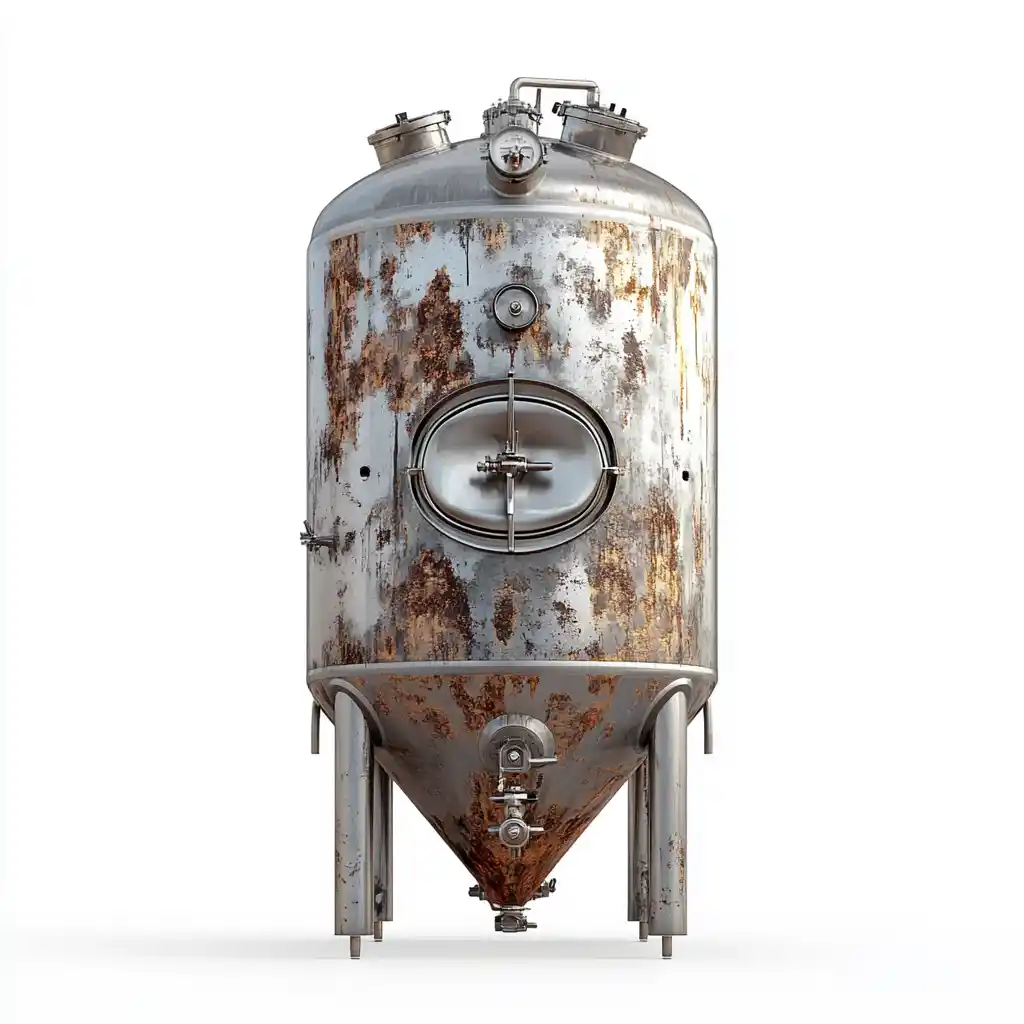
- Potential Equipment Damage: The risk of equipment damage from caustic cleaners increases with improper use, such as incorrect concentrations, excessive temperatures, or inadequate rinsing. This can lead to stress corrosion cracking in stainless steel.
- Stress Corrosion Cracking: This phenomenon occurs when stainless steel is exposed to caustic substances in the presence of mechanical stress and chloride ions, leading to micro-cracks that may propagate over time. These cracks compromise the structural integrity of brewing equipment, potentially causing leaks, contamination, and costly repairs.
- Mitigation Strategies:
- Proper Usage: Use caustic cleaners judiciously, limiting their concentration and frequency.
- Regular Inspections: Implement routine equipment inspections to detect early signs of corrosion.
- Safety Measures: Ensure staff are trained and equipped with proper protective gear.
Choosing the Right Cleaner for Your Brewery
Homebrewers:
For homebrewers, non-caustic brewery wash generally the preferred choice. These cleaners are safer to handle, reducing the risk of personal injury and equipment damage. Non-caustic options are effective for typical homebrewing cleaning tasks, ensuring that equipment remains in good condition without the need for specialized safety protocols. If a homebrewer decides to use caustic cleaners, it is imperative to adhere strictly to safety guidelines and verify that all equipment is compatible with such aggressive chemicals to prevent potential hazards.
Commercial Breweries:
In commercial breweries, caustic cleaners are commonly used as the standard cleaning agent. Their cost-effectiveness and efficiency in removing heavy organic soils make them suitable for large-scale operations. Commercial breweries typically have strict protocols in place and utilize equipment designed to withstand the rigorous nature of caustic cleaning solutions. However, integrating non-caustic alternatives can be beneficial for addressing specific challenges like biofilm removal and enhancing overall safety and sustainability. By incorporating non-caustic cleaners into their regimen, commercial breweries can optimize their cleaning processes while mitigating some of the risks associated with caustic substances.
Final Thoughts
The exploration of non-caustic versus caustic cleaners illuminates the complex considerations behind brewery hygiene. By understanding the chemical mechanisms, impacts on equipment, beer quality, and safety, brewers can make informed decisions that align with their operational needs and values. Non-caustic cleaners emerge as a holistic solution, embodying the synergy between advanced cleaning technology and environmental stewardship, paving the way for a new era in brewery cleanliness.